In 2005 realiseerde Saint-Gobain Weber haar eerste 3D-geprinte muur en inmiddels rollen er dagelijks producten uit de betonprinter in de Eindhovense fabriek. Ontdek de vele mogelijkheden van deze printtechniek en hoe bouwwerken nu ook de hoogte in gaan. Een gesprek met Peter Paul Cornelissen, business unit manager 3D Printing, en Udo Snijer, productmanager beton.
Met duurzaam beton en 3d-printen de hoogte in

“Vanwege onze expertise op het gebied van mortels”, begint Udo Snijer, “kregen we begin deze eeuw van de University of California de vraag of we een betonmortel konden ontwikkelen om 3D te printen. De basale eis was dat de eerste geprinte lagen het gewicht konden dragen van de lagen die er daarna op werden geprint. Anders kun je per keer slechts enkele lagen printen, voordat alles in elkaar zakt. In 2005 resulteerde dit in de eerste 3D-geprinte betonnen muur, waarmee we aantoonden dat zowel het materiaal als het proces kansrijk waren.”
Het was Theo Salet, professor aan de TU Eindhoven, die in 2015 besloot te onderzoeken hoe het 3D-betonprintproces meer geautomatiseerd kon worden. Daarna werd in samenwerking met onder andere Saint-Gobain Weber en BAM Infra in 2017 de eerste 3D-geprinte fietsbrug gerealiseerd in Gemert. Deze acht meter lange betonnen brug werd geprint in het lab van de TU Eindhoven.
Vervolgens richtte Saint-Gobain Weber een eigen productlocatie in. Deze eerste commerciële betonprintfabriek in Europa werd in 2019 geopend in Eindhoven, waarna de ontwikkelings- en productieactiviteiten in 3D-betonprinten steeds verder werden geïntensiveerd.
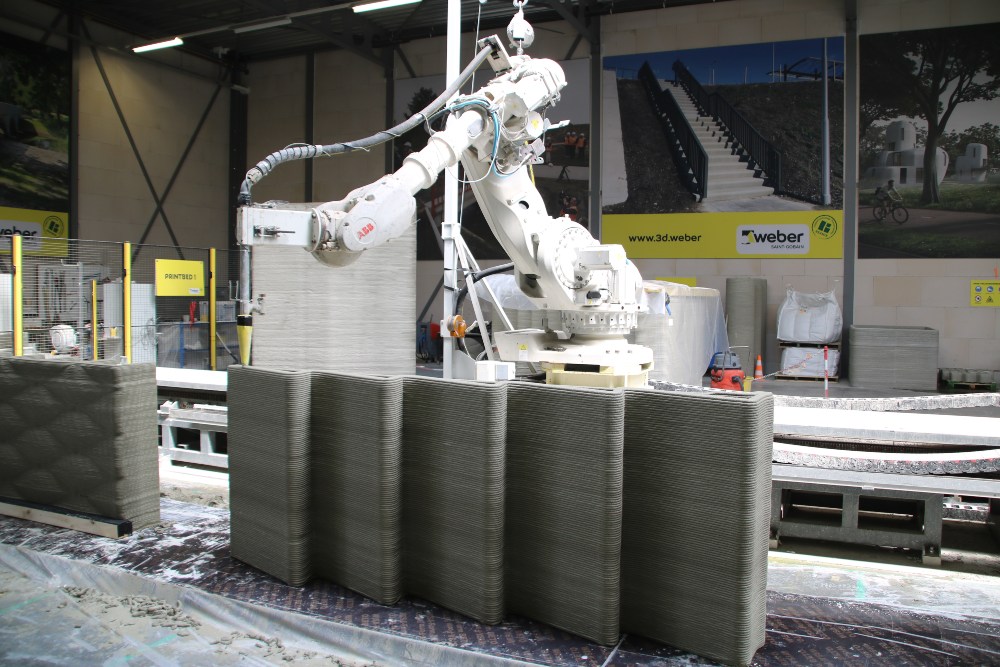
Uniek proces
Peter Paul Cornelissen legt uit hoe het proces werkt: “Eerst wordt met 3D-software een ontwerp van bijvoorbeeld een brug, trap of constructief element gemaakt. Dit bestand ontvangen wij van onze klanten. Vaak maken wij dan, samen met de klant, een vertaalslag naar een ontwerp dat we kunnen printen. Dit uiteindelijke ontwerp wordt in laagjes verdeeld - het slicen van het ontwerp - waarna we deze laagjes omzetten in een robotcode. Daarmee kan de robot vanuit een digitale vorm de laagjes printen tot een fysiek object.”
Om de kwaliteit van de eindproducten te kunnen garanderen, werd het 3D Mortel Platform ontwikkeld. Cornelissen vervolgt: “Dit platform waarborgt het proces, waardoor we structureel en consistent de benodigde kwaliteit kunnen leveren. We gebruiken droge betonmortel die speciaal voor het 3D-betonprinten is ontwikkeld en volgens een KIWA-certificaat wordt geproduceerd en gecontroleerd. Vervolgens monitoren we het hele printproces met sensoren en kwaliteitsmetingen. Deze genereren de benodigde data om het volledige printproces te controleren. Na het printen controleren we na 7 en 28 dagen de sterkteontwikkeling van de geprinte objecten. Pas als dat hele proces met succes is afgerond, krijgt de klant een certificaat waarop staat dat het betonnen object voldoet aan alle afgesproken waarden. Met dit hele proces zijn wij uniek in de wereld.”
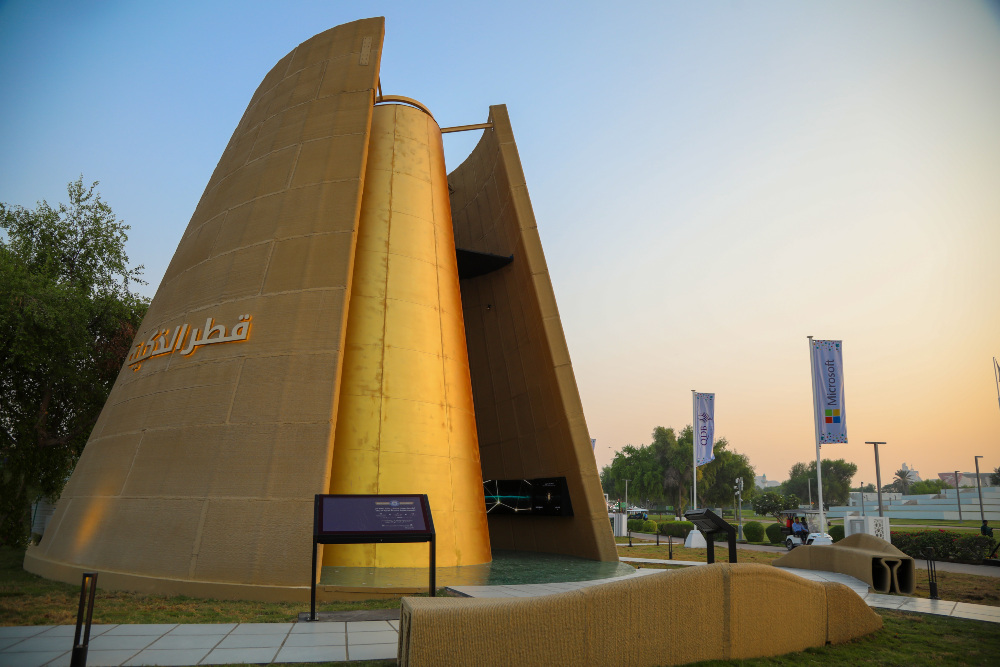
Robotisering
Door het volledig gedigitaliseerde proces, neemt de foutmarge af, kunnen objecten snel worden geleverd en verminderen de werkzaamheden op locatie aanzienlijk. Cornelissen: “Door de robotisering zijn er ook veel minder mensen nodig. Vrijwel dagelijks worden nu objecten geproduceerd, waarbij het printproces voor een groot deel of in zijn geheel geautomatiseerd verloopt. Een voorbeeld zijn de taludtrappen, waarvoor een configurator op de website staat. Met deze handige tool kun je eenvoudig zelf een taludtrap ontwerpen. Daarnaast produceren we objecten op projectbasis, zoals de toren voor de Doha Expo 2023 in Qatar (foto boven). Wereldwijd bezitten wij de meeste kennis en praktijkervaring op het gebied van 3D-betonprinten. Kijk maar naar alles wat we realiseren: vijftig tot zestig taludtrappen, zes bruggen, de Milestonehuizen en verschillende torens. Dat alles heeft ons een schat aan kennis en ervaring opgeleverd over materiaal, proces en de benodigde eindkwaliteit van constructieve producten.”
Vrijwel alle vormen kunnen worden geprint. Ook vormen die met traditionele bekistingen vaak onmogelijk waren. Zo kun je probleemloos dertig skate-elementen maken en die allemaal iets variëren. Bij traditioneel gestort beton is dat onbetaalbaar. Cornelissen: “3D-betonprinten is een perfecte bouwmethode als er allemaal unieke vormen of afmetingen nodig zijn. Het toverwoord hierbij is parametrisch ontwerpen. Daarbij worden modellen of ontwerpen automatisch gegenereerd op basis van parameters als afmetingen, materiaaldikte of geometrie. Hiermee kan de printrobot eindeloos variëren.”
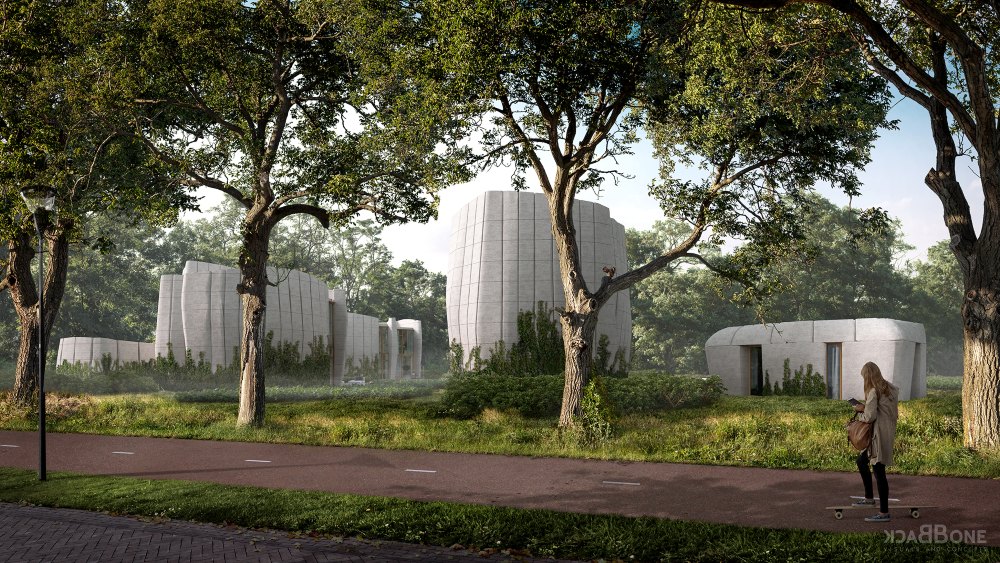
Duurzaamheid
Het 3D-betonprinten kent ook diverse duurzame aspecten. Cornelissen: “We printen de contouren van een object en als het voor de sterkte nodig is, printen we tegelijkertijd in de holtes een structuur om de krachten te kunnen dragen. We printen dus alleen beton waar dat nodig is en dat resulteert in een CO2-reductie van vijftig tot zeventig procent.” Udo Snijer gaat verder: “We onderzoeken ook of we het cement in betonmortel geheel kunnen vervangen. De eerste stap daarin is gezet met Weber 3D Eco, een product dat 49 procent minder CO2 uitstoot dan de traditionele mortel.”
“3D-betonprinten is een technologie die nog door de markt omarmd moet worden”, aldus Cornelissen. “Als je kijkt naar de acceptatiecurve van nieuwe producten of technologieën zit je bij de meeste 3D-geprinte producten nog aan het begin. Onze 3D-geprinte taludtrappen worden wel met grote regelmaat besteld. Er zijn steeds meer klanten, de ware early adapters, die het als kans zien om hiermee vandaag aan de slag te gaan.”
Een recent fraai uithangbord werd gevormd door een skatepark in Parijs, dat tijdens de Olympische Spelen voor iedereen toegankelijk was. Ook opmerkelijk is het vervolg van het Milestone-project (foto boven), waar in 2025 hogere huizen worden gebouwd. Zo zijn er nog meer spraakmakende projecten (zie www.3D.weber) en daarmee willen Cornelissen en Snijer de komende periode zorgen voor groei van het 3D-betonprinten in de Benelux. Cornelissen heeft er alle vertrouwen in: “Steeds meer opdrachtgevers gaan er de voordelen van inzien.”
Blijf nog beter op de hoogte van al ons nieuws en abonneer je op de wekelijkse nieuwsbrief van Stedebouw & Architectuur.
Tekst: Peter Bekkering
Reactie toevoegen